Layoutoptimierung erklärt an einem Anwendungsfall
Anhand des Use Cases eines Kompressorenherstellers möchten wir das Vorgehen bei einer Layoutoptimierung und Layoutplanung näher beleuchten. Das Unternehmen ist ein mittelständischer Hersteller von Kolben- und Schraubenkompressoren. Ziel der Layoutoptimierung ist es, die gesamte innerbetriebliche Wertschöpfungskette des Unternehmens optimal zu gestalten.
Die Fertigung umfasst verschiedene Bereiche, darunter die Herstellung des Gehäuses bzw. des Grundkörpers der Kompressoren, den Spritzguss von Kunststoffgehäusen und die Produktion von Drehteilen. Alle weiteren Bauteile und Komponenten werden als Zukaufteile bezogen und fließen direkt in die Montage der Fertigerzeugnisse ein.
Je nach Art des Kompressors werden unterschiedliche Bearbeitungsschritte an verschiedenen Stationen durchgeführt. Diese Schritte müssen sorgfältig geplant und koordiniert werden, um einen reibungslosen Materialfluss und eine effiziente Produktion zu gewährleisten. Durch die detaillierte Layoutoptimierung können Engpässe identifiziert und Optimierungspotenziale genutzt werden, was letztlich zu einer höheren Produktivität und Kosteneffizienz führt.
Gestaltung und Optimierung des Layouts
Mögliche Bezugsquellen für benötigte Werte und Informationen sind Arbeitspläne, Fertigungsaufträge, Bewegungsdaten und Stücklisten. Hiermit können bspw. Prozessschritte, Materialflüsse oder die Anzahl an benötigten Maschinen ermittelt werden. Auf Basis dieser Datenerfassung wurden die Wertströme erstellt. Die Abbildung zeigt exemplarisch einen solchen Wertstrom zur Herstellung eines Kolbenkompressors.
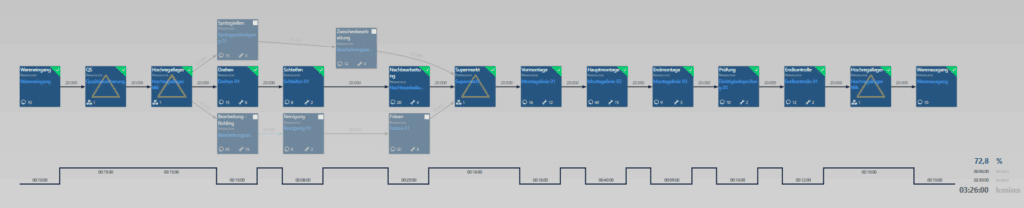
Dimensionierung der Flächen und Struktur in der Layoutoptimierung
Auf Grundlage des zukünftigen Produktionsprogramms und einer umfassenden Kapazitätsplanung wurde die Dimensionierung der Flächen in Plavis visTABLE® durchgeführt. Dabei wurden die Flächen zunächst in die Funktionsbereiche Logistik, Produktion und Montage unterteilt. Diese klare Strukturierung ermöglicht eine gezielte und effiziente Layoutoptimierung der einzelnen Bereiche.
Neben den drei Hauptbereichen, die in diesem Anwendungsfall im Fokus stehen, wurde an der Gebäudefront ein Verwaltungstrakt eingerichtet. Dieser Verwaltungstrakt wird an dieser Stelle nicht weiter definiert, da der Schwerpunkt auf den operativen Bereichen liegt. Durch diese detaillierte Planung wird sichergestellt, dass alle relevanten Aspekte der Produktion und Logistik berücksichtigt werden, um eine optimale Nutzung der verfügbaren Flächen zu gewährleisten.

Vom Blocklayout zum optimalen Detaillayout
Die Feinplanung begann im Bereich der Logistik, die in vier verschiedene Teilbereiche unterteilt wurde: den Wareneingang mit Hochregallager, die Qualitätssicherung, den Supermarkt und den Warenausgang mit Hochregallager. Diese detaillierte Unterteilung ermöglicht eine präzise Steuerung und Überwachung der logistischen Abläufe.
Im Anschluss wurde der Bereich der Produktion detailliert festgelegt. Die Grundlage dafür bildet neben dem Grundriss der erstellte Fertigungsprozess, der dem Wertstrom entnommen ist. Die Blocklayouts der einzelnen Stationen wurden so gestaltet, dass der Materialfluss möglichst optimal verläuft. Dies gewährleistet eine effiziente und reibungslose Produktion.
Der Materialfluss wird in einem späteren Abschnitt des Use Cases im Detail analysiert und erläutert. Aufgrund der verschiedenen Varianten der zu produzierenden Kompressoren enthält das Layout unterschiedliche Stationen. Dabei wird berücksichtigt, dass nicht jede Station für die Herstellung jeder Variante benötigt wird. Diese Flexibilität im Layout ermöglicht eine Anpassung an die spezifischen Anforderungen der Produktion.
Durch diese strukturierte und detaillierte Planung wird sichergestellt, dass sowohl die logistischen als auch die produktionstechnischen Abläufe effizient und effektiv gestaltet sind. Dies trägt maßgeblich zur Optimierung des gesamten Produktionsprozesses bei.
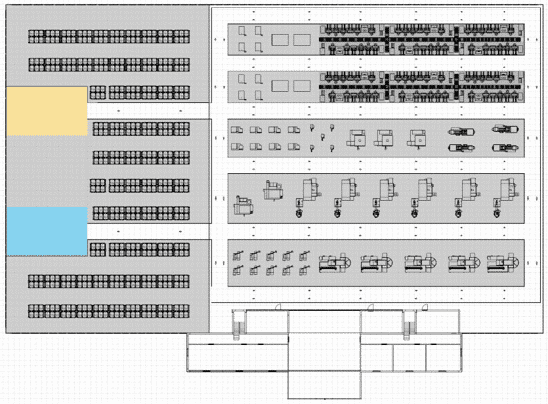
Detailplanung ergonomischer Arbeitsplätze in 3D
Anschließend wurden die Produktionsanlagen modelliert und den entsprechenden Stationen zugeordnet. Dies gilt ebenso für die Dichtigkeitsprüfung und die Endkontrolle der Montage. Für die Montagelinien wurden spezifische Montageplätze modelliert, die ebenfalls in diesem Schritt in das Layout integriert wurden. Es ist wichtig zu beachten, dass es sich bei den modellierten Anlagen nicht zwingend um die tatsächlich verwendeten Anlagen handelt, da der Modelkatalog von Plavis visTABLE® nur eine begrenzte Variantenvielfalt bietet. Daher sind alle Anlagen als schematische Darstellungen zu betrachten, die die grundlegenden Funktionen und Platzanforderungen repräsentieren.
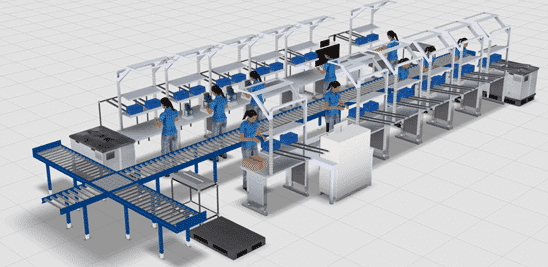
Vom Layout zur detaillierten Layoutoptimierung
Bislang bestand der Mehrwert des bis hierhin entwickelten Layouts darin, dass man einen besseren Eindruck von der tatsächlich benötigten Fläche einschließlich der Verkehrswege sowie eine ansprechende optische Darstellung erhalten hat. Der eigentliche Mehrwert wird jedoch erst jetzt geschaffen. Dies geschieht durch die Verbindung der Prozesse, die im Wertstrom abgebildet sind, mit dem Layout.
Durch die physische Verortung der im Wertstrom hinterlegten Ressourcen kann der Materialfluss nun quantifiziert und anschließend optimiert werden. Sämtliche Quelle-Senke-Beziehungen sind, wie im hier dargestellten Anwendungsfall, nun hinterlegt und in Blau visualisiert. Diese detaillierte Darstellung ermöglicht es, den Materialfluss präzise zu analysieren und gezielte Maßnahmen zur Verbesserung der Effizienz und Reduzierung von Engpässen zu ergreifen.
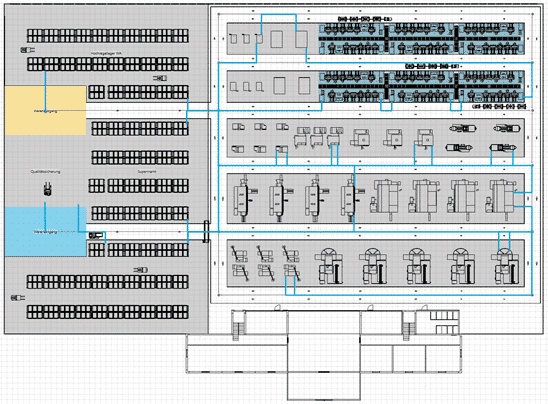
Heatmap zur Identifikation potenzieller Engpässe
Die Analysefunktionen in Plavis visTABLE® umfassen die Netzbelastung, die Logistikbewertung und die Flächenbilanz. Zunächst wird die Netzbelastung untersucht. Diese Analyse basiert auf der Auslastung des gesamten Transportnetzes durch alle im System vorhandenen Produktgruppen. Dabei werden die einzelnen Abschnitte des Transportnetzes separat betrachtet und anhand der Flussmenge der transportierten Produkte bewertet. Die Ergebnisse dieser Bewertung werden visuell durch eine Farbskala dargestellt, die von grün (geringe Belastung) bis rot (hohe Belastung) reicht.
In dem hier dargestellten Anwendungsfall ist deutlich zu erkennen, dass der Transportweg zu und von dem Supermarkt besonders stark belastet ist. Dies liegt an dem hohen Aufkommen von Transporten, da die Produkte nach jedem Bearbeitungsschritt in den Supermarkt gebracht werden. Diese detaillierte Analyse ermöglicht es, Engpässe im Transportnetz zu identifizieren und gezielte Maßnahmen zur Optimierung des Materialflusses zu ergreifen.
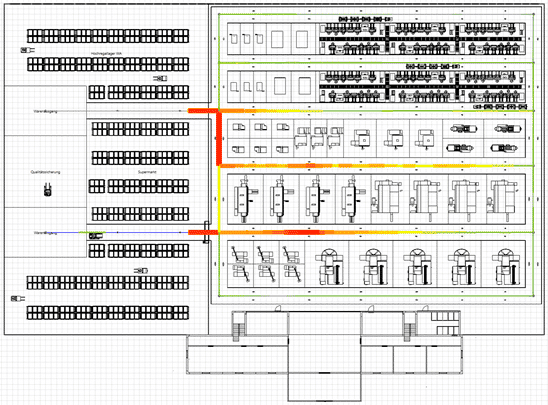
Bewertung des Materialflusses durch Key Performance Indicators
Als nächstes wird die Logistikbewertung in den Fokus genommen. Diese Bewertung bezieht sich auf die detaillierte Analyse des Materialflusses entlang des gesamten Wertstroms. Um die Ergebnisse dieser Bewertung anschaulich darzustellen, konzentrieren wir uns auf eine spezifische Produktfamilie – die Kolbenkompressoren. Der Materialfluss kann visuell abgebildet werden, wodurch die Verknüpfungen zwischen den einzelnen Stationen deutlich sichtbar werden. Dies ermöglicht es, erste Optimierungspotenziale zu identifizieren. Der Materialfluss verläuft entlang des Wertstroms über das Transportnetz zu den verschiedenen Stationen der Logistik, Produktion und Montage. Der aktuelle Zustand des Materialflusses wird anhand von Key Performance Indicators (KPIs) wie beispielsweise der Gesamtlänge des Transportwegs bewertet. Diese KPIs bieten eine klare Grundlage für die Identifikation und Umsetzung von Verbesserungsmaßnahmen.
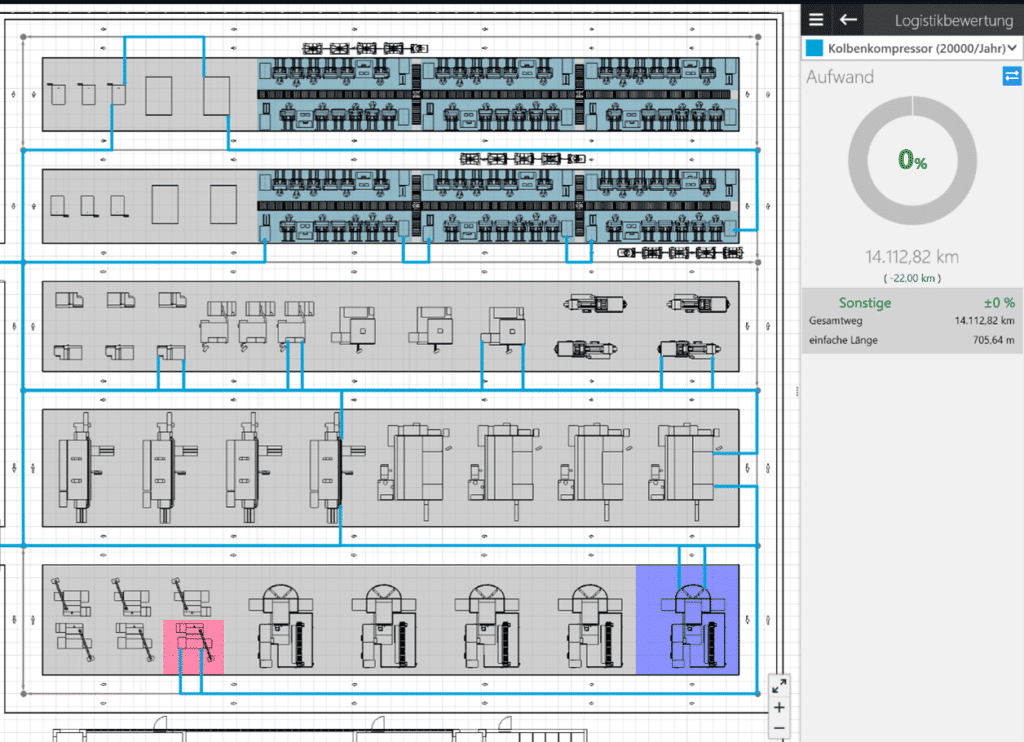
Effiziente Layoutoptimierung durch intuitives Drag-and-Drop-Verfahren
Durch das gezielte Verschieben einzelner Blöcke innerhalb des Blocklayouts kann der Materialfluss auf anschauliche und effektive Weise optimiert werden. In dem hier dargestellten Anwendungsfall wurde die Position der Reinigungseinheit (rot markiert) so verändert, dass sie näher an das Bearbeitungszentrum (blau markiert) herangerückt ist. Diese Anpassung führte zu einer Reduzierung des Materialflusses um 10 %. Die Verlagerung der Reinigungseinheit ermöglicht somit eine effizientere und zeitsparendere Abwicklung der Arbeitsprozesse, was sich positiv auf die Gesamtproduktivität auswirkt.
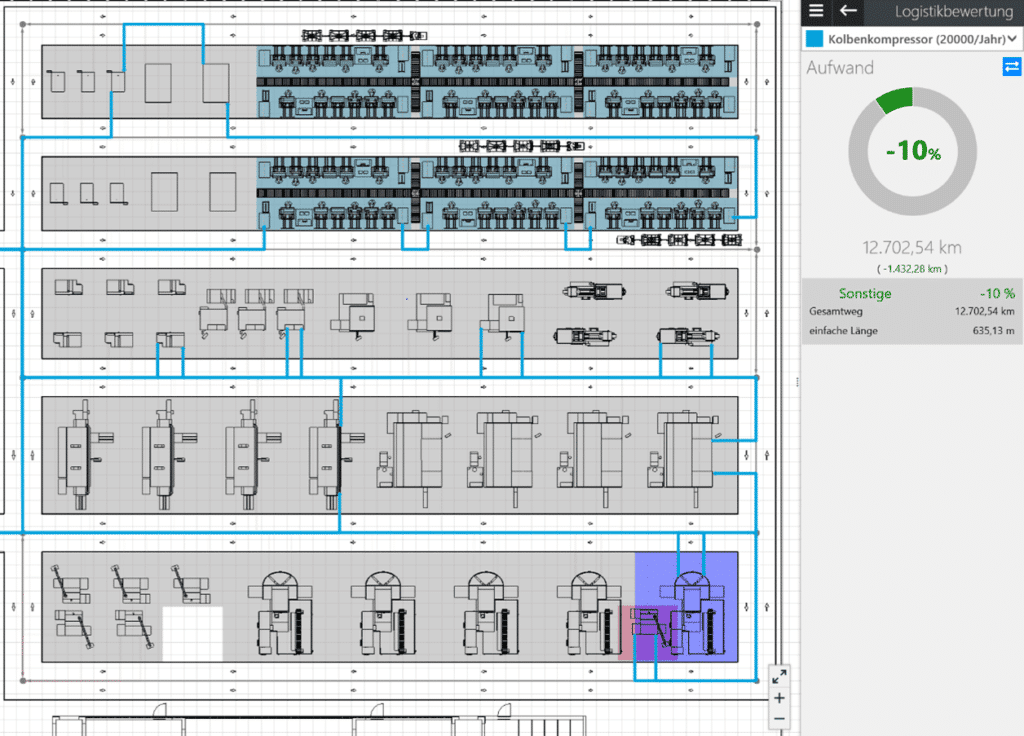
Wir unterstützen Sie bei der Optimierung und Planung Ihres Layouts
Unsere Experten verfügen über eine langjährige und umfassende Erfahrung in der Layoutoptimierung sowie der Materialflussoptimierung. Mit ihrem fundierten Wissen und ihrer Expertise sind sie in der Lage, maßgeschneiderte Lösungen zu entwickeln, die den spezifischen Anforderungen und Bedürfnissen Ihres Unternehmens gerecht werden. Wir legen großen Wert auf eine enge Zusammenarbeit mit unseren Kunden, um sicherzustellen, dass die vorgeschlagenen Maßnahmen nicht nur effizient, sondern auch nachhaltig sind. Zögern Sie nicht, uns zu kontaktieren – wir freuen uns darauf, gemeinsam mit Ihnen innovative und zukunftsorientierte Konzepte zu erarbeiten!
Folgen Sie gerne auch unserem Linkedin-Newsletter für Inhalte wie diesem!
Ihr Ansprechpartner
Dr. Florian Bross
Managing Partner
+49 89 413276720
info@bross-consulting.com