Layout optimization explained using a use case
Based on the use case of a compressor manufacturer, we would like to take a closer look at the procedure for layout optimization and layout planning. The company is a medium-sized manufacturer of piston and screw compressors. The aim of layout optimization is to optimize the company’s entire internal value chain.
Production covers various areas, including the manufacture of the housing or base body of the compressors, the injection molding of plastic housings and the production of turned parts. All other parts and components are sourced as purchased parts and are incorporated directly into the assembly of the finished products.
Depending on the type of compressor, different processing steps are carried out at different stations. These steps must be carefully planned and coordinated to ensure a smooth material flow and efficient production. Detailed layout optimization allows bottlenecks to be identified and optimization potential to be exploited, which ultimately leads to higher productivity and cost efficiency.
Design and optimization of the layout
Possible sources of reference for the required values and information are work plans, production orders, movement data and parts lists. These can be used, for example, to determine process steps, material flows or the number of machines required. The value streams were created on the basis of this data collection. The illustration shows an example of such a value stream for the production of a piston compressor.
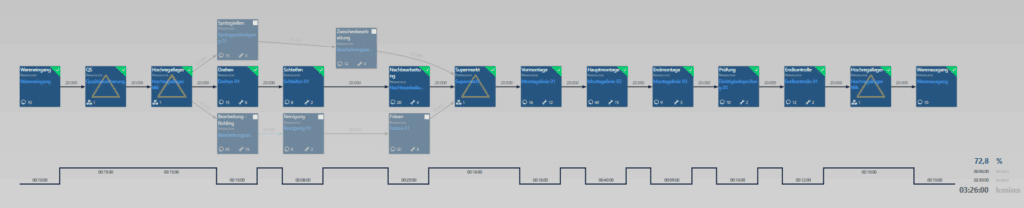
Dimensioning of areas and structure in layout optimization
Based on the future production program and comprehensive capacity planning, the areas were dimensioned in Plavis visTABLE®. The areas were initially divided into the functional areas of logistics, production and assembly. This clear structure enables targeted and efficient layout optimization of the individual areas.
In addition to the three main areas, which are the focus of this use case, an administrative wing has been set up at the front of the building. This administrative wing is not defined further here, as the focus is on the operational areas. This detailed planning ensures that all relevant aspects of production and logistics are taken into account in order to guarantee optimum use of the available space.

From block layout to optimal detailed layout
Detailed planning began in the logistics area, which was divided into four different sub-areas: incoming goods with high-bay warehouse, quality assurance, supermarket and outgoing goods with high-bay warehouse. This detailed subdivision enables precise control and monitoring of the logistics processes.
The production area was then defined in detail. In addition to the floor plan, the basis for this is the production process created, which is taken from the value stream. The block layouts of the individual stations were designed to optimize the material flow. This ensures efficient and smooth production.
The material flow is analyzed and explained in detail in a later section of the use case. Due to the different variants of the compressors to be produced, the layout contains different stations. It is taken into account that not every station is required for the production of every variant. This flexibility in the layout enables adaptation to the specific requirements of production.
This structured and detailed planning ensures that both logistical and production processes are efficient and effective. This contributes significantly to the optimization of the entire production process.
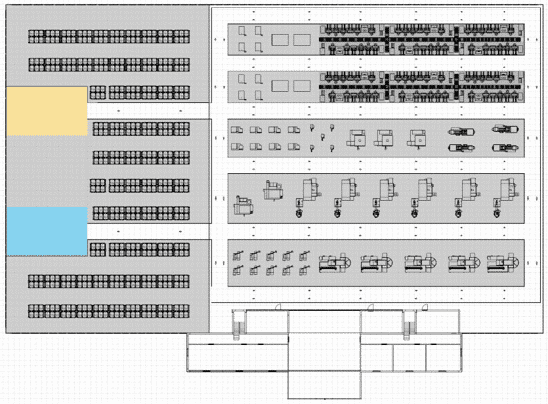
Detailed planning of ergonomic workstations in 3D
The production systems were then modeled and assigned to the corresponding stations. This also applies to the leak test and the final assembly check. Specific assembly stations were modeled for the assembly lines, which were also integrated into the layout in this step. It is important to note that the systems modeled are not necessarily the systems actually used, as the Plavis visTABLE® model catalog only offers a limited number of variants. Therefore, all systems should be considered as schematic representations that represent the basic functions and space requirements.
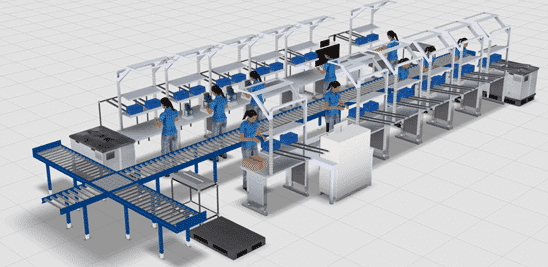
From layout to detailed layout optimization
So far, the added value of the layout developed up to this point has been that it has given a better impression of the area actually required, including the traffic routes and an appealing visual representation. However, the actual added value is only now being created. This is achieved by linking the processes mapped in the value stream with the layout.
By physically locating the resources stored in the value stream, the material flow can now be quantified and subsequently optimized. All source-sink relationships are now stored and visualized in blue, as in the use case shown here. This detailed representation makes it possible to precisely analyze the material flow and take targeted measures to improve efficiency and reduce bottlenecks.
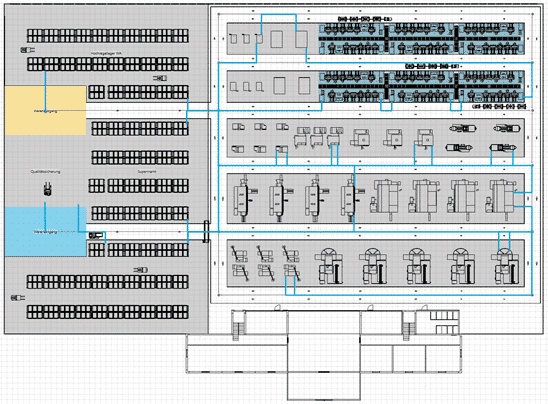
Heat map to identify potential bottlenecks
The analysis functions in Plavis visTABLE® include the network load, the logistics evaluation and the area balance. The network load is analyzed first. This analysis is based on the utilization of the entire transport network by all product groups in the system. The individual sections of the transportation network are considered separately and evaluated based on the flow rate of the transported products. The results of this evaluation are displayed visually using a color scale ranging from green (low load) to red (high load).
In the use case shown here, it is clear to see that the transport route to and from the supermarket is particularly heavily loaded. This is due to the high volume of transportation, as the products are taken to the supermarket after each processing step. This detailed analysis makes it possible to identify bottlenecks in the transport network and take targeted measures to optimize the material flow.
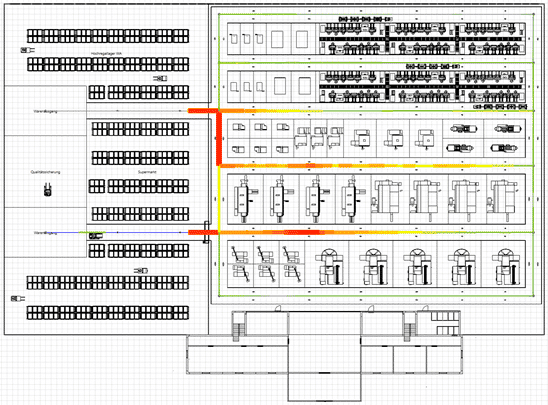
Evaluation of the material flow using key performance indicators
The next step is to focus on the logistics assessment. This evaluation refers to the detailed analysis of the material flow along the entire value stream. To illustrate the results of this assessment, we focus on a specific product family – reciprocating compressors. The material flow can be mapped visually, making the links between the individual stations clearly visible. This makes it possible to identify initial optimization potential. The material flow runs along the value stream via the transportation network to the various logistics, production and assembly stations. The current status of the material flow is evaluated using key performance indicators (KPIs) such as the total length of the transport route. These KPIs provide a clear basis for identifying and implementing improvement measures.
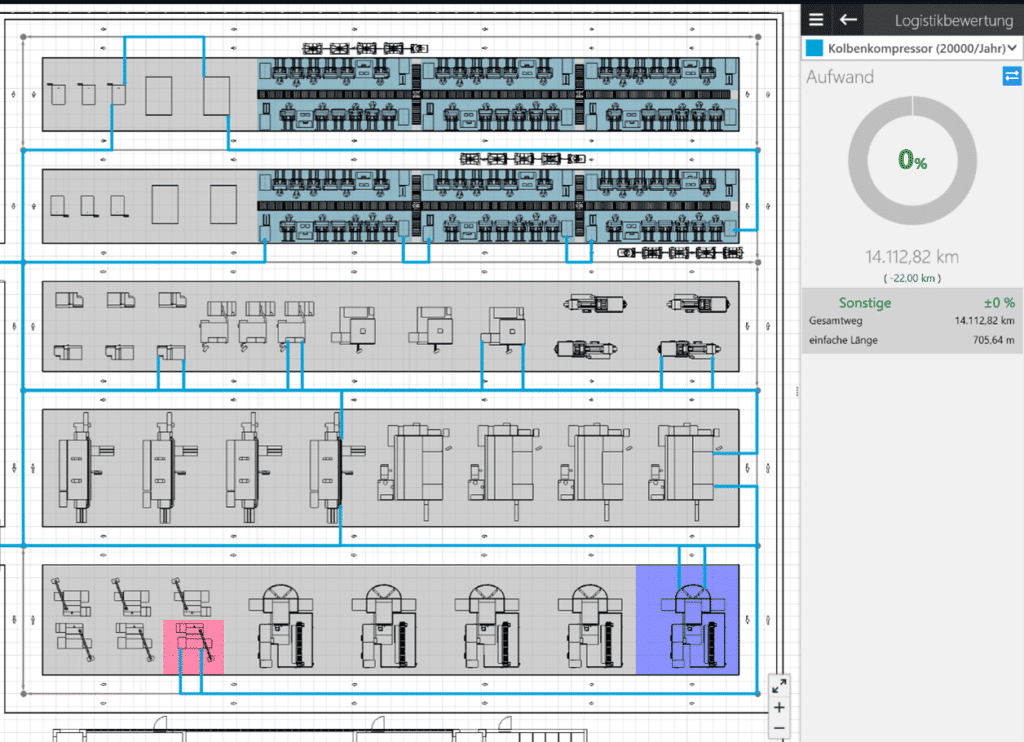
Efficient layout optimization through intuitive drag-and-drop process
By moving individual blocks within the block layout, the material flow can be optimized in a clear and effective way. In the application shown here, the position of the cleaning unit (marked in red) was changed so that it was moved closer to the machining center (marked in blue). This adjustment led to a 10% reduction in the material flow. The relocation of the cleaning unit therefore enables more efficient and time-saving handling of the work processes, which has a positive effect on overall productivity.
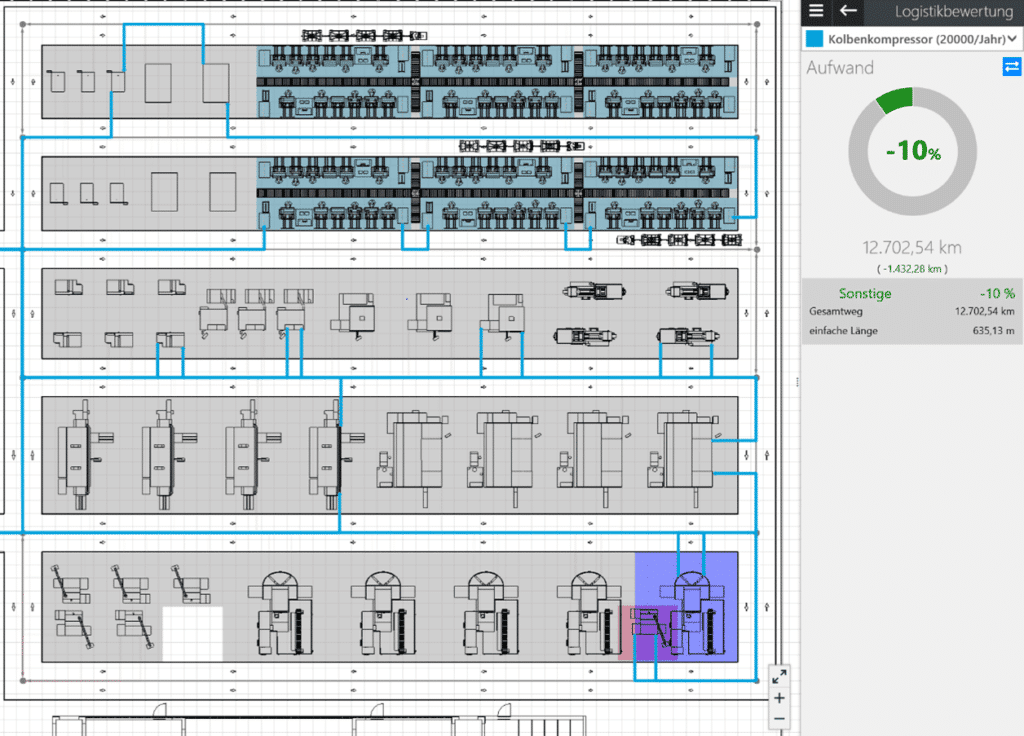
We support you in optimizing and planning your layout
Our experts have many years of extensive experience in layout optimization and material flow optimization. With their in-depth knowledge and expertise, they are able to develop customized solutions that meet the specific requirements and needs of your company. We attach great importance to working closely with our customers to ensure that the proposed measures are not only efficient but also sustainable. Do not hesitate to contact us – we look forward to working with you to develop innovative and future-oriented concepts!
Your contact person
Dr. Florian Bross
Managing Partner
+49 89 413276720
info@bross-consulting.com