Digital twin – application and advantages
A digital twin is suitable for use in logistics and factory planning. It is a digital method for improving your planning processes. A digital twin is the virtual mirror image of a machine, a production line or an entire factory. This digital replica, which can be an entire production facility, not only supports the analysis, design or evaluation of processes, but also helps with the overall planning of production or logistics processes.
Acting instead of reacting with digital twins
The knowledge we gain from a digital twin allows us to react to any conceivable situation in real time. To this end, the collected operating data is processed, understood, evaluated and utilised. To realise this, raw data is evaluated using data analytics and simulations and forecasts are created. This not only facilitates and improves the planning of new systems, but also enables service to be raised to the next level. The simulations can be used to predict maintenance cases or necessary servicing, which makes implementation easier and reduces costs.
Advantages in planning through digital twins
However, the digital twin offers enormous advantages, particularly when it comes to process design. For example, the material flow can be optimised without having to restructure systems and machines in reality. This not only saves time and costs, but also shows the best possible production process. This applies to both the shop floor level and the planning process.
Towards Industry 4.0 with the digital twin
The digital twin also represents a major leap towards Industry 4.0, as it makes a significant contribution to the digitalisation of your company. In a further step, it is possible to operate even more digitally by “viewing” the digital twin “live” in the empty production/logistics hall via AR & VR applications. This creates initial impressions and positioning or processes can be further adapted or optimised. In summary, it can be said that the concept of the digital twin can be developed into the perfect business process and is indispensable in the course of further advancing digitalisation in production and logistics.
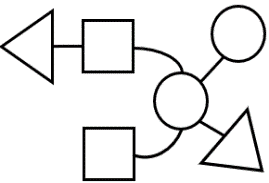
Component twin
The basic unit of the digital twin is called a component twin and represents a replica of a single component of the twin that has a key function. Although the definition of the partial twin is the same as that of the component twin, the partial twin refers to components with an irrelevant meaning.
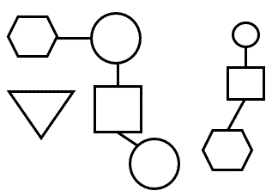
Asset twin
If two or more individual components work together, this is referred to as an asset. The asset twin represents the next level up from the digital twin. It can be used to examine the interactions between the individual components, thereby analysing their interaction and identifying potential for improvement
System twin
The system twin or unit twin combines several asset twins into an overall system. This system provides information about the interactions between the asset twins and can be used to identify potential for performance improvements.
Process twin
The process twin represents the macro level of the digital twin. It combines several systems with each other and shows how the systems or all units work together and whether this happens synchronously. For example, the process twin can represent an entire production plant. This is intended to maximise efficiency. It can also show how delays from one system affect another. In this way, the change in overall effectiveness can be analysed using various scenarios.
Difference between a digital twin and a classic simulation
The definition of simulation and digital twin already reveal significant differences. Nevertheless, a clear distinction must be made as to which of the two is actually involved. Classic simulation tends to be used for new planning where no current status is available. For this reason, simulations can only be used to make theoretical predictions about potential events in the event of changes. Furthermore, the integration of real-time data is certainly possible, but in reality this is very time-consuming. A digital twin, on the other hand, can show what is happening at the present moment and in the future within the processes of the physical twin. For this reason, the digital twin tends to be created for existing systems. Nevertheless, it should be noted that a classic simulation and a digital twin are only as good as the quality of the data they work with.
Digital model
The digital model is generally regarded as a digital replica of an existing or planned object that does not automatically exchange data between the physical and digital object. The model has more or less information about the physical object and can contain mathematical models of new products or other models of the physical object. Data is only exchanged manually, which means that the change of state of the physical object does not affect the digital counterpart and vice versa.
Digital shadow
The digital shadow can generally be seen as a virtual replica of all relevant data from production, development and the areas within the system boundary. In contrast to the digital model and the twin, a one-way data flow takes place between the physical and digital object. A change in the status of the physical object results in a change in the digital counterpart, but not vice versa.
Digital Thread
The digital thread describes a type of connection between all sub-models and extends across the entire product life cycle. It also acts as an interface for these and can integrate information from other IT systems (e.g. CRM). It also ensures traceability and makes it possible to search backwards for problems with a component and determine the cause. This enables optimisation across the entire value creation process.
System
A system can generally be regarded as a construct of elements that are related to each other. The system boundary acts as a boundary between the system and the system environment. However, a system should never be considered in general, but only in different types of systems. Examples of systems would be